Druckgefässförderer zur pulsationsarmen Dosierung und Förderung
von K.Schneider veröffentlicht im Jahrbuch Dampferzeugertechnik 1989, S. 506-516
1. Einleitung (Ausgangslage)
Das Dosieren von Schüttgütern ist invielen Fällen mit dem Transport des Materials zur Abgabestelle verbunden. Dabei muß oft von einer Aufgabestelle auf mehrere Abgabestellen verteilt werden. Hierbieten sich kombinierte Verfahren zur gleichzeitigen Dosierung und Förderung an. Ein bekanntes und oft genutztes Transportverfahren ist die pneumatische Förderung von Schüttgütern.
Die Dosierung, d.h. die Gutaufgabe in die Förderleitung erfolgt in den allermeisten Fällen mechanisch durch Schnecken- oder Zellenradzuteiler. Die Kombination beider Verfahren hat sich in vielen Einsatzfällen bewährt und ist Stand der Technik. Erhöhte Anforderungen an Dosiergenauigkeit und weitgehende Pulsationsfreiheit können damit jedoch nicht abgedeckt werden.
Die Versorgung von Steinkohlenzündbrennern [1, 2] ist beispielsweise mit deroben erwähnten Standardkombination nicht mehr betreibbar. EntsprechendeVersuche mit einer Zellenraddosierungbrachten keine befriedigenden Ergebnisse. Da die Flammenüberwachung auf lntensitätsschwankungen mit der Abschaltung des Brenners reagierten, sind selbsthöherfrequente Schwankungen, wie siedurch die unregelmäßige Kammerentleerung bei Zellenrädern hervorgerufen werden für eine sichere Anlagenfunktion untragbar.
Daher wurde ein neues Dosiersystementwickelt und gebaut. Dieses Systemkann nicht nur dosieren und fördern, sondern ist auch in der Lage, verschiedeneVerbrauchs- oder Eintragstellen von einerAufgabestelle aus zu versorgen. Andersals die oben beschriebene Standardkombination arbeitet das neue MDS-Verfahren (Mehrfach-Dosier-System) rein pneumatisch, d.h. es gibt weder mechanischeDosierorgane noch mechanische Verteiler.
Der grundsätzliche Aufbau sowie Erfahrungen mit einem solchen Mehrfach-Dosier-System (MDS) sollen hier beschrieben werden.
2. Ansprüche an eine pneumatische Dosierförderung (Aufgabe)
Welche Ansprüche werden denn nunan Dosierung und Förderung gestellt ?
Eine pneumatische Dosierförderungsollte neben hoher Mengenkonstanz weitere Ansprüche befriedigen. Hier sind vorallem folgende Kriterien zu nennen:
- möglichst geringer apparativer und regeltechnischer Aufwand
- niedrige Betriebs- und Energiekosten
- Zuverlässigkeit und geringer Verschleiß des Systems
- kontinuierliche Versorgung mehrererEmpfangsstellen von einer Aufgabe-stelle aus
- Zu- und Abschalten einzelner Empfangsstellen während des Anlagenbetriebes.
Im Hinblick auf die pneumatische Dosierförderung läßt sich dazu folgendesfeststellen:
Der apparative und regeltechnische Aufwand ist natürlich für volumenabgrenzende Dosierer wie Zellenrad oderSchnecke am geringsten, jedoch lassen dieunvermeidbaren Dosierstromschwankungen den Einsatz dieser Aggregate nichtimmer zu. Die Betriebs- und Energiekosten für eine rein pneumatische Dosierförderung sind vergleichsweise geringerals die für z.B. mechanische Dosierung mitanschließender pneumatischer Förderung. Da rein pneumatische Dosierförderer keine im Feststoffstrom drehenden Teile enthalten, ist deren Verschleiß niedriger und die Zuverlässigkeit entsprechend höher.
Insbesondere gilt das zuvor Gesagtefür Dichtstrom-Förderungen wegen derdort auftretenden relativ hohen Beladungen. Unter Beladung ist hier das Verhältnis von Feststoff- zu Gas-Massenstrom zu verstehen.
Die kontinuierliche Versorgung mehrerer Empfangsstellen von nur einer Aufgabestelle aus ist bei der pneumatischenDosierförderung ohne nachgeschalteteVerteiler möglich. Sind die Widerständeder parallelgeschalteten Rohrleitungengleich, fließen auch gleiche Massenströme an Gas und Feststoff durch die einzelnen Stränge. Das Zu- und Abschalten einzelner Förderstränge vergrößert den Einsatzbereich, da Zwischenzustände oder Teillasten relativ einfach angefahren werden können.
3. Vorstellung des MDS-Systems (Lösung)
Um die vorgenannten Ansprüche befriedigen zu können, wurde ein Druckgefäßfördersystem konzipiert, welches in Bild 1 dargestellt ist.
Dieses System erlaubt die kontinuierliche Versorgung einer oder mehrerer Empfangsstellen von einem Aufgabebehälteraus und ist insbesondere für die Dosierförderung feinkörniger und pulvrigerSchüttgüter wie z. B. Kohle, Asche oderKalkprodukten geeignet.
Bild 1: Verfahrensschema der Dosieranlage
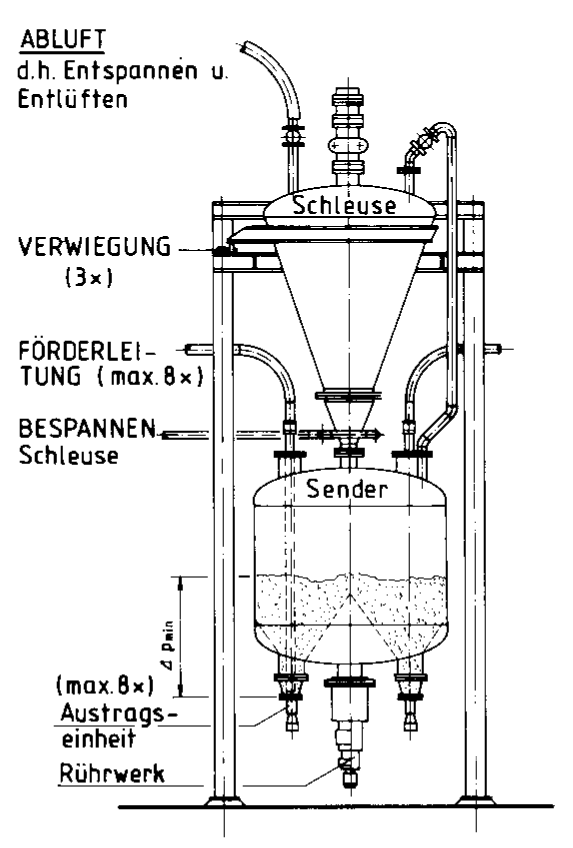
Bild 2: Grundsätzlicher Aufbau des Mehfach-Dosier-Systems
Die im Bild 1 gezeigte Anlage wurde für die Versorgung von Kohlenstaub-Zündbrennern mit fein aufgemahlenemSteinkohlenstaub ausgelegt. Die wichtigsten technischen Daten der Anlage sind in Tafel 1 zusammengefaßt. Die Gesamtanlage und Erfahrungen mit der Zündfeuerung wurden bereits an anderer Stelle veröffentlicht [1, 2].
Insgesamt 6 (maximal 8) Brenner können von einem Dosiersystem versorgtwerden. Bild 2 zeigt schematisch den Aufbau des Mehrfach-Dosier-Systems und ermöglicht so die Zuordnung zum Verfahrensschema Bild 1.
Jede Förderleitung versorgt einen Brenner. Da die Brenner untereinander gleich sind, mithin auch die gleicheBrennstoffmenge benötigen, wurden dieRohrleitungswiderstände sorgfältig angeglichen. Jede Förderleitung hat eine eigene Differenzdruckmessung auf die im folgenden noch näher eingegangen wird.
Anzahl der Förderleitungen | 1 – 8 |
Durchsatz pro Förderleitung | 200 – 3500 kh/h |
Beladung | 10 – 60 kg/kg |
Förderleitungslänge | 10 – 60 m |
Druckverlust der Förderleitung | 0,5 – 4 bar |
möglicher Gegendruck | bis 20 bar |
Gasgeschwindigkeit (Austritt) | 8 – 20 m/s |
mittlerer Partikeldurchmesser | 0,04 – 1 mm |
Schüttdichte | 250 – 1.600 kg/m3 |
Tabelle 1: Technische Daten zum Mehrfach-Dosier-System MDS
Alle Förderleitungen münden in sogenannten Austragseinheiten, welche gleichmäßig verteilt am Boden des Sendegefäßes montiert sind.
Über pneumatisch betätigte Düsenkönnen die einzelnen Stränge zu- oder abgeschaltet werden. Für eine gleichmäßigeVerteilung des Schüttgutes im Sender sorgt ein elektromotorisch angetriebenesRührwerk. Der Senderinhalt wird über Niveausonden kontrolliert. Der Druck im Sender wird mittels Druckaufnehmern überwacht.
Um einen kontinuierlichen Betrieb der Anlage zu ermöglichen, wird über demSendegefäß ein sogenannter Schleusbehälter als Druckwechseleinheit angeordnet. Dieser sorgt bei Anforderungdurch die Niveauüberwachung des Dosiersenders für Materialnachschub ins Sendegefäß.
Bevor auf den genauen Taktablauf desFördersytems eingegangen wird, sollen zunächst die Austragseinheit und derenRegelverhalten beschrieben werden.
3.1. Beschreibung der Austragseinheit
Die Austragseinheit ist das eigentlicheHerzstück des Dosierförderers und wird am unteren Teil des Druckgefäßes montiert. Bild 3 zeigt den schematischen Aufbau einer Austragseinheit, die durch zweiMerkmale gekennzeichnet ist:
- Die Aufteilung der zugeführten Gas-menge in zwei Teilgasströme (Austragsgas VA und Fördergas VF)
- die mittels pneumatischem Zylinderhöhenverstellbare Düse
Durch die Aufteilung des Gesamtgasstromes in Fördergas VF und Austragsgas VA ist die Möglichkeit einer Durchsatzänderung gegeben. Bei konstantem Gasstrom wächst die pro Zeiteinheit ausgetragene Feststoffmenge mit steigendemAustragsgasanteil. (Da das Trägergas nicht unbedingt immer Druckluft seinmuß, wird im folgenden allgemein vonGasstrom gesprochen).
Der einstellbare Durchsatzbereich ist vom Material abhängig und liegt bei ca.
2:1 bis 4:1.
Bild 4 zeigt exemplarisch den Massenstrom, die Beladung und den korrespondierenden Behälterdruck für einen Kohlenstaub, abhängig vom Austragsgasanteil. Die verstellbare Düse dient zur Absperrung der Förderleitung vom Behälter. Dazu wird die Düse mittels eines pneumatischen Zylinders direkt auf dieFörderleitung gefahren. So wird der Feststoffstrom unterbrochen und die Leitungkann freigeblasen werden. Der Abstand von Boden und Förderleitungsanfang wird so dimensioniert, daß größereFremdteile nicht eingetragen werden und zu Verstopfungen führen können. DerBehälter bleibt dabei unter Druck, so daß durch einfaches Auffahren der Düse die Feststofförderung wieder fortgesetzt werden kann.
Die Absperrung einzelner, beliebigerFörderleitungen ermöglicht so z.B. auchdas Fahren von Teillasten, d.h. einzelne Brenner oder Brennergruppen können wahlweise zu- oder abgeschaltet werden.Die stillgesetzten Förderleitungen der Brenner können dabei durch die geschlossene Düse ständig mit Spülgas VS (z.B.zur Kühlung) versorgt werden.
Erläuterungen zu Bild 3:
1 = Fördergefäß
2 = Förderleitung
3 = Dichtung
4 = Anschluß für Austragsgas / Bespanngas
5 = Anschluß für Fördergas / Spülgas
6 = Höhenverstellbare Düse (Auf-Zu)
7 = Pneumatikzylinder für Düsenverstellung
8 = Ausstragboden mit Ringspalt und Führungsfläche für Austragluft
9 = Feststoff / Schüttgut
Bild 3: Die Austragseinheit
3.2. Änderung und Überwachungdes Feststoffdurchsatzes
Der Feststoffdurchsatz in der Förderleitung läßt sich bei vorstehend beschriebener Austragseinheit in sehr einfacherWeise ändern und überwachen. Mechanisch bewegte Teile oder Fluidisierung derSchüttung mit all ihren bekannten Nachteilen sind daher nicht erforderlich.
Bild 3 zeigt, daß der ankommendeGasstrom (Summengas) in zwei Teilgas-ströme (Fördergas und Austragsgas) aufgespalten wird. Das Fördergas VF tritt direkt zentrisch in das untere Ende der Förderleitung ein und übernimmt eine Träger- und Verdünnungsfunktion für dasmit dem seitlichen Austragsgasstrom VA einfließende Schüttgut. Dabei wird auf eine Fluidisierung bewußt verzichtet. DerMaterialfluß in die Förderleitung wirdzum einen durch den Entzug der Stützkräfte für die Materialschüttung entlangdes Bodens und zum anderen durch die Impulsübertragung des mit relativ hohenGeschwindigkeiten ringförmig austretenden Gasstrahles übernommen.
Um über den gesamten Regelbereichstabile Förderbedingungen in den Feststoffleitungen verwirklichen zu können,wird die Gesamtgasmenge V•Σ konstant gehalten. Dies bedeutet konstante Geschwindigkeit am Leitungsaustritt undunterschiedliche Drücke bzw. Geschwindigkeiten am Förderleitungsanfang. DieBeladung, d. h. das Verhältnis von Feststoff zu Gasdurchsatz, wird variiert. Ein Beispiel hierfür ist in Bild 4 angegeben.Man erkennt, daß eine nahezu lineare Abhängigkeit zwischen Feststoffdurchsatz
und dem Verhältnis Austragsgas zu Gesamtgas besteht. Gleiches gilt für den korrespondierenden Behälterdruck.
Bild 4: Durchsatzdiagramm für eine Förderleitung
Bild 5: Feststoffmassenstrom als Funktion des Behälterdruckes
Die gezeigten Kurven sind reproduzierbar anzufahren, aber von dem zu dosierenden Feststoff abhängig. Entsprechende Eichkurven müssen aber für jedenFeststoff aufgenommen werden. Schüttgutabhängig verändert sich auch die Form der Kurve, d. h. manche Eichkurven sind nicht mehr linear, sondern haben z. B. einen parabolischen Verlauf.
Auch die Grenzen für den maximalen Austragsgasanteil sind von Material zuMaterial unterschiedlich. Während zum Beispiel körnige Schüttgüter mit Austragsgasanteilen von bis zu 95 % gefördertwerden können, liegen die Grenzen fürfeinkörniges Gut bei ca. 80 % oder nochdarunter. Überschreitet man diese Grenzwerte, so kann die Förderleitung verstopfen.
Bild 5 zeigt den Feststoffmassenstromals Funktion des Behälterdruckes. Hier wurde bei Voreinstellung des Austragsgasanteils der korrespondierende Behälterdruck stabilisiert. Dazu wird, wie in Bild 1 gezeigt, das Ersatzgas durch den Anschluß,,Nachbespannen" dem Dosiersender zugeführt. Der Abzug des Feststoffes nachunten in die Förderleitungen vergrößertnämlich das Gasvolumen oberhalb der Schüttung und führt bei fehlender Durchströmung von unten zu Druckabsenkungen. Diese Druckschwankungen beeinflussen direkt den Massendurchsatz, können aber durch Zugabe von Ersatzgasoberhalb der Schüttung aufgefangen werden.
Der Massenstrom durch die Förderleitung wird, wie in Bild 5 dargestellt, dadurch sehr konstant und die Güte der Dosierung nochmals verbessert. Mit einer überlagerten Druckregelung lassen sichfeststoffabhängige Dosierfehler von weniger als 2-5 % erreichen.
3.3. Betriebsablauf beim Mehrfach-Dosier-System MDS
Bei Materialanforderung durch eineoder mehrere Verbrauchsstellen öffnen die Düsen der entsprechenden Austragseinheiten nach Aufschalten der zugeordneten Gasströme.
Vorbedingung hierfür ist ein ausreichender Druck im Dosiersender. Wird ein bestimmter Füllstand, in Bild 2 als ∆Pmin gekennzeichnet, unterschritten, muß Material nachgezogen werden. Dazu wird die drucklose Schleuse mit Material aus einem Vorratsbunker befüllt (vergleiche Bild 6). Anschließend wird der Schleusbehälter bis zur Druckgleichheitmit dem Dosiersender bespannt. Dannöffnet sich die Überströmleitung zwischen Schleuse und Sender sowie die Materialabsperrklappe und das Materialfließt in den Dosiersender. Nach Ende des Schleusvorganges wird das Schleusgefäß wieder vom Sendegefäß abgekoppelt und auf Umgebungsdruck entspannt.
Insbesondere bei feinen kohäsiven Stäuben kann der verdichtete Staub schlecht oder gar nicht aus dem Schleusgefäß auslaufen. Wirksame Abhilfe schafft hier ein besonderes Bespannverfahren für die Schleuse. Dabei wird z.B. schon während des Befüllens auf eine Gasanreicherung im Schüttgut geachtet.Erst dieses, an einer Versuchsanlage entwickelte und erprobte Verfahren, hat einen reibungslosen und störungsfreien Gesamtablauf der Förderung ermöglicht.
Durch Verwiegung der Dosierbehälterwird der gesamte Dosierstrom für alle Leitungen erfaßt. Bei mehreren Förderleitungen werden die einzelnen Stränge getrennt über Differenzdruckmessungen kontrolliert.
4. Erste Ergebnisse mit MDS
4.1. Druckmessungen undPulsationen
Bild 6: Druckverlauf bei MDS
Bild 6 zeigt den schon erwähnten Druckverlauf im Dosiersystem. Neben den Behälterdrücken ist dort auch der Differenzdruck einer Förderleitung nebst zugehörigem Flammenwächtersignal aufgezeichnet. Da bei diesem Aufschrieb dieDruckstabilisierung noch nicht realisiertwar, sieht man deutlich den Einfluß der Behälterdruckschwankungen auf die Differenzdruckmessung. EntsprechendeMassenstromschwankungen (bis ca. 8 %)waren die Folge. Durch die Druckstabilisierung konnten, wie bereits unter 1.3.2.beschrieben, die Dosierfehler entscheidend verringert werden.
Die Förderung selbst war, wie ein Blickauf Bild 6 zeigt, äußerst pulsationsarmund in keinem Fall Ursache für ein Ansprechen des Flammenwächters.
4.2. Durchsatzleistung und -verteilung
Bild 7: Durchsatzverteilung beim6-fach-Dosierssystem
In Bild 7 sind die Förderleistungen dereinzelnen Stränge (6fach Dosiersystem)aufgetragen. Für die Einstellung der Förderleistung war die Brennerstabilität ausschlaggebend, so daß bestimmte Abwei-chungen durchaus beabsichtigt waren. Die Mindestschütthöhe im Behälter und die damit verbundene Druckdifferenz zwischen den einzelnen Austragseinheiten gestattet nämlich je nach Feststoff eine Vertrimmung von bis zu 15 % der jeweiligen Durchsatzleistungen.
4.3. Betriebsablauf und Zuverlässigkeit
Die einzelnen Leitungen werden mittels einer Differenzdruckmessung überwacht. Eine Steuerung oder Regelung mitdem Differenzdruck als Istwertgeber istStand der Technik [3], wurde im vorliegenden Fall jedoch nicht realisiert. Die Überwachung beschränkt sich auf möglicheDruckschwankungen in der Leitung, d.h.sich ankündigende Verstopfungen. Diesewerden signalisiert und bewirken ein Zufahren der Düse bei gleichzeitigerSpülgaserhöhung. Die beginnende Verstopfung kann so in jedem Fall aufgelöstwerden. Eine Störung durch blockierteFörderleitungen wurde bisher nicht beob-achtet.
Auch das Nachziehen von Material aus der Schleuse in den Dosiersender ver-läuft mit dem erwähnten Steuerungsab-lauf problemlos. Sollte trotzdem einmaleine Schleusenfüllung nicht vollständig inden Dosierbehälter entleert werden, kann das Schleusprogramm wiederholt und das verbliebene Schüttgut beim zweitenDurchlauf umgeschleust werden.
Insgesamt waren die Erfahrungen mitder neuen Dosierförderung sehr positivund der Betrieb ist bis heute (Zeitpunktder Veröffentlichung) weitestgehend störungsfrei verlaufen.
Bild 8: Pneumatischer Dosiersender
5. Weitere Anwendungen deskombinierten Dosier- und Fördersystems und Ausblick
5.1. Transport
Um die beschriebenen Vorzüge desDosiersystems auch für reine Transport-arbeiten nutzen und gleichzeitig die Herstellungskosten senken zu können, wurdeeine Bauartreihe entwickelt. Eigene Messungen und neuere Untersuchungen anderer Autoren [4] haben gezeigt, daß nachoben austragende Druckgefäßfördererhöher beladen werden können als solche mit Bodenauslaß.
Diese Förderer verfügen daher ebenfalls über einen Austragsboden und dieAufteilung in Fördergas, Austragsgas undErsatzgas. Der Boden ist jedoch einfacherausgebildet und die Förderleitung wirdaußerhalb des Gefäßes mittels Ouetschventil oder Kugelhahn abgesperrt. Bild 8zeigt den schematischen Aufbau eines solchen Senders.
Eingesetzt werden diese Aggregatezum pneumatischen Transport von Flug-und Bettasche in Feuerungsanlagen sowie für die Förderung von Kalkproduktenund Inertmaterial (Sand). Durch je eineDrosselstelle in Förder- und Austragsleitung kann bei der Inbetriebnahme dieEinstellung des gewünschten Materialdurchsatzes erfolgen.
Weiterhin wird durch Einstellung derSpaltweite zwischen Förderleitungsbeginn und Boden die maximal eintretendeKorngröße so begrenzt, daß die Förderleitung nicht verstopfen kann und dieseBrocken entweder zerrieben und dann gefördert bzw. von Hand ausgeräumt werden können.
5.2. Dosierförderung unter extremen Bedingungen
Gilt es bei bestimmten Prozessen hohe Drücke und hohe Temperaturen zu überwinden, ist das Dosiersystem ebenfalls erfolgreich einzusetzen.
(c) 2002 Ingenieurbüro Klaus Schneider Köln
Denkt man z. B. an die Kohlevergasungim Flugstrom, wo rückgeführter Koksgrusgegen Drücke von bis zu 20 bar und Temperaturen von bis zu 300°C verteilt eingetragen werden muß, bietet sich das Mehrfach-Dosier-System geradezu an. Erfahrungen in den genannten Druck- undTemperaturbereichen sind vorhanden. Wie schon erwähnt, muß das Fördergasnicht unbedingt Luft sein, es wurden Erfahrungen mit z. B. Argon, Stickstoff undHeißdampf als Trägermedium gesammelt. Hier kommt der Vorzug der pulsationsarmen Förderung ebenfalls voll zur Geltung, da die Prozesse und laufendenReaktionen unter Umständen sehr empfindlich auf Druck-und/oder Massenstromschwankungen reagieren können.
5.3. Ausblick
Mit dem pneumatischen Dosiersystem MDS ist der Bedarfsfall einer pulsationsarmen, hochkonstanten Dosierförderung abgedeckt worden. Die Betriebssicherheit und Zuverlässigkeit, verbundenmit dem Vorteil der Mehrfachdosierung,wurden in der Praxis nachgewiesen. DasSystem bietet durch seine hohe Flexibilität auch in anderen Bereichen Vorteile und kann leicht an die jeweiligen Verhältnisse angepaßt werden.
Schrifttum
Rennert, K.D.: KohlenstaubgefeuerterZündbrenner. BWK 34(1982), S. 131-135
Rennert, K.D.: Kohlenstaubzündfeuerung: Anwendung, Betriebsergebnisse, Wirtschaftlichkeit -BWK 36 (1984), S. 217-222
Heep, D.: Dosierung von pneumatischtransportierten Schüttgütern mittels Druckdifferenzsteuerung, ZKG 33 (1980), S.373-374
Jones, M.G., D. Mills und J.S. Mason: A Comparison of the performance of Topand Bottom Discharge Blow Tank systems, Bulk solids handling 7 (1987), S.701-706